Aluminum and composite materials boost self driving vehicle on the road
Now the main structure of electric vehicles are all made of aluminum, or more than 80% of the materials used are aluminum, and less than 20% of the rest are composite materials. Of course, steel and other materials are indispensable. The so-called all aluminum manufacturing is to use aluminum for all parts that can be made of aluminum alloy under the existing technology, ensuring safety and riding comfort. At present, aluminum is the most cost-effective material for making electric vehicles. Of course, there are also composite materials. However, the price of composite materials is high, and the problem of waste recycling and recycling has not been completely solved, which is not conducive to the recycling of materials. Therefore, in the future of automobile materials, aluminum will undoubtedly play a leading role before 2030. From 2031 to 2035, aluminum and composite materials will be equally divided, and composite materials will probably become the leading role after 2035.
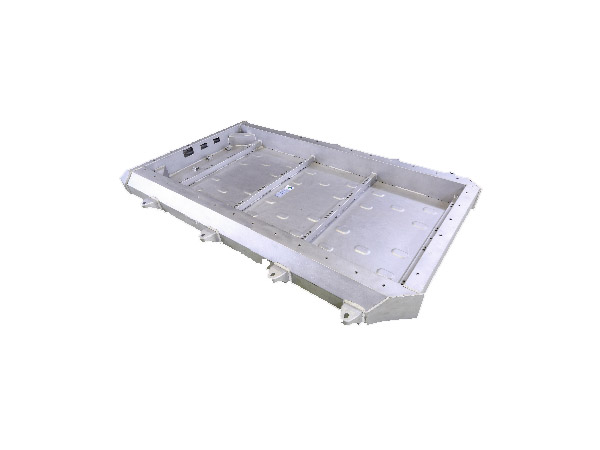
Shanghai will take the lead in letting driverless cars run all over the street
According to foreign media, the Financial Times website reported on September 17, 2019 that Shanghai will be China's first city to issue licenses to allow automatic driving vehicles to transport goods and passengers on the city streets. China's Shanghai automobile manufacturing company, German BMW automobile company and online car Hailing company didi travel are among the first enterprises to be awarded "demonstration application" licenses for intelligent network vehicles, Xinhua reported.
In recent years, some auto manufacturers around the world have invested heavily in the development of automatic driving technology. It seems that this technology will lead the global automobile transportation industry. Six or seven cities in the United States, such as Phoenix, San Francisco, Detroit, Pittsburgh and Palo Alto, have already issued licenses.
Permanent magnet motor will be eliminated
Today's electric vehicles all use permanent magnet motor. One of its main disadvantages is that it has back EMF, which hinders the current in the conductor, resulting in the vehicle unable to achieve high speed. If you want to increase the speed, you must reduce the magnetic field to reduce the back EMF. However, this requires electrical energy. As a result, the efficiency of the motor decreases and the battery time is shortened. The second major drawback is that the permanent magnet will be demagnetized due to the heating of the motor This requires a strong cooling system. When the electric vehicle starts to slow down suddenly, it means that the magnet is overheated and can not run normally. The test results show that a new motor for electric vehicle invented in Russia in 2018 can still maintain good operation performance at 150 ℃, while the current permanent magnet motor stops running at 100 ℃. Its advantages are as follows: the motor does not use permanent magnet but copper coil to generate running magnetic field; the endurance of the car is increased by 15%; it will not stop suddenly due to overheating, and does not need complex and expensive cooling system; the price is only 1 / 3 ~ 1 / 4 of that of traditional permanent magnet motor, and the price of new machine is about 8600 yuan / set, while the price of traditional permanent magnet motor is about 32260 yuan / set. The Electrical Engineering Department of Moscow University of technology was invented by Bauman.
The body will be part of the battery
In the current electric vehicle, the battery tray is the largest and heaviest structural part, accounting for about 1 / 5 ~ 1 / 4 of the total vehicle mass. If there is no separate battery module, it will be much more convenient. Scientists at chamers Polytechnic in Sweden really came up with the idea that it's possible to make the body part of the battery. In this way, the body is not only a load-bearing part, but also an important part of the battery, which can greatly reduce the net weight of the car. This is a big leap forward, with a maximum weight loss of up to 50%.