There are nine steps in the extrusion process of industrial aluminum profiles
Most of the industrial aluminum profiles are developed according to the existing needs of users, and some industries have strong development capabilities, For example, rail vehicle manufacturing industry, automobile manufacturing industry, etc., but some small industries lack self-development ability, or have not realized that industrial aluminum profiles can be used to replace existing materials. Therefore, it is necessary for production enterprises to assist users in developing alternative industrial aluminum profiles. To achieve this, it is necessary to go out and make a detailed investigation on the materials used in all walks of life, and find out the suitable ones to be replaced by aluminum profiles Through these development, we can expand the market demand of industrial aluminum profiles, especially the development of large-scale industries. Increasing the market demand can reduce the fierce competition situation faced by large and extra large extrusion lines under construction. Improve the overall production technology of industrial aluminum profiles. Most industrial aluminum profiles have strict requirements on material, performance and dimensional tolerance. Although the profit of industrial aluminum profile is higher than that of architectural aluminum profile, its production difficulty is relatively large, and the technical requirements are also higher. Especially, the production technology of complex large-scale industrial aluminum profile with flat width and thin wall still has a large gap with foreign countries.
1. Selection of raw materials
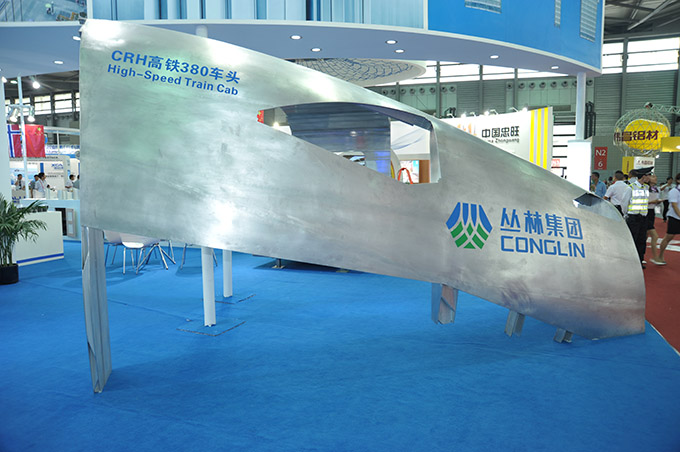
Industrial aluminum profile is a kind of industrial frame profile which is obtained by heating aluminum bar and extrusion molding, while aluminum bar is made by melting and casting aluminum ingot, which is called industrial aluminum profile raw material; and raw material will directly affect the performance of industrial aluminum profile.
The production of aluminum bar needs high technical requirements and industry standards to ensure the product performance of industrial aluminum profiles
① : content of active impurities;
② : alloy composition;
③ : melt superheat temperature;
④ : diversion mode;
⑤ The melt moves relative to the crystal surface;
⑥ : cooling rate;
⑦ : casting speed of 6063 aluminum bar;
2. Aluminum rod heating
Aluminum bar heating treatment to ensure the temperature control, extrusion outlet temperature, on-line quenching temperature and so on.
3. Mold design
The industrial aluminum profile is the final product of aluminum bar through extrusion molding after heating, and the mold is an instrument with high-precision specifications designed according to the requirements, which is used to extrude the profile products with the required specifications and cross-section. The design and maintenance of the mold should pay attention to the following points:
① : the structure involved in the mold should first meet the production requirements, but also conform to the common sense of physics and mechanics, so as to ensure that the products produced can reach the performance used.
② The material selection and hardness of the die should be appropriate to avoid deformation, scratch and other hard injuries in the extrusion process, which will affect the final product quality.
③ It is necessary to clean and check the die frequently and repair the problem in time to avoid scratch, burr and other hard damage in the extrusion production process, which will seriously affect the quality of industrial aluminum profiles.
4. Extrusion of industrial aluminum profiles
At present, the standard of extrusion press used for 6063-T5 industrial aluminum profiles is 1300-1600 tons. The above standards can meet the normal production of 6063-T5 industrial aluminum profiles.
Key points for attention in extrusion process of industrial aluminum profiles:
① Temperature control: for extrusion production, extrusion temperature is the most basic and key process factor. Extrusion temperature has great influence on product quality, production efficiency, die life and energy consumption.
② Extrusion speed: the extrusion speed must be controlled carefully during extrusion. Extrusion speed has an important influence on the deformation heat effect, deformation uniformity, recrystallization and solution process, mechanical properties and surface quality of products.
③ On machine quenching: 6063-T5 quenching is to keep Mg2Si which is solid dissolved in the base metal out of the mold hole at high temperature and then quickly cooled to room temperature. The cooling rate is usually proportional to the content of strengthening phase. The minimum cooling rate of 6063 alloy is 38 ℃ / min, so it is suitable for air cooling quenching. The cooling intensity can be changed by changing the rotation number of fan and fan, so that the temperature of products before tension straightening can be reduced to below 60 ℃.
5. Straightening correction of industrial aluminum profiles
There will be a certain deviation after the extrusion of industrial aluminum profiles. After forming, straightening machine should be used to straighten and correct the industrial aluminum profiles just extruded to the required tolerance range. Straightening correction must be completed by straightening machine to ensure its accuracy.
6. Artificial aging
The hardness of extruded aluminum profile is low before aging, so it can not be used as finished product. Therefore, generally speaking, the strength must be improved by aging.
Production process control:
① Ingot temperature control: the temperature of ingot should be measured before extrusion, and then it can be put into production after meeting the process requirements.
② On line quenching process: solution quenching is the basic premise of aging, without solution quenching, aging is meaningless. Therefore, the on-line quenching process (air quenching, air mist quenching, water quenching, etc.) should be selected according to the ingot brand, section wall thickness, extrusion speed and quenching equipment conditions at the outlet of the extruder, so as to ensure that the quenching cooling rate meets the quenching sensitivity requirements of the alloy.
③ Setting and control of aging furnace temperature: generally, there is a certain error between the aging furnace temperature and the aging furnace surface temperature. When setting the surface temperature, it should be set according to the actual temperature of the furnace, and pay close attention to the fluctuation of the aging furnace temperature.
④ Aging and heat preservation: aging shall be carried out in strict accordance with the process requirements, and the holding time shall be appropriate to prevent insufficient hardness caused by under aging or over aging.